Early Dubilier mica capacitor vs. the two Leyden jars it replaced.


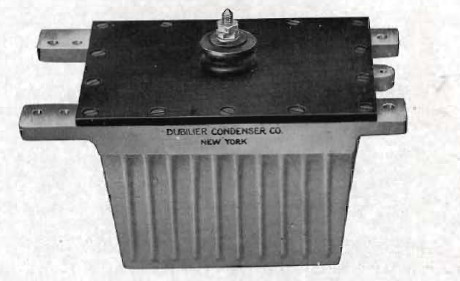
Leyden jars:
By now, everyone kind of knows the first capacitor was the Leyden jar (or Leiden), discovered by Ewald Georg von Kleist in 1745. Peter van Busschenbroeck of the U. Of Leyden rediscovered the jar the next year and ended up with the credit. He was a teacher of science of some fame, and he documented the Leyden jar in a way von Kleist had not
An early Leyden jar had the capacitance in the one nF range, depending on size and glass thickness. This gave rise to the first unit of capacitance, the "jar", about 0.0011 uF, used by the British navy well into the 1940s. Some used foil as the inner conductor, first tin, then copper, and some used liquids such as salt water. Ben Franklin worked with Leyden jars and found that parallel glass plate capacitors also worked. These became known as "Franklin Squares", although the idea was not original to Franklin.
Many scientists (commonly known as electricians) played around with Leyden jar over the years and around the beginning of the 20th century the Leyden jar was finally put to use. They were the first high-voltage capacitors used in early radio telegraphy transmitters. Some systems used as many as 50 jars in series and parallel configurations. Amateur radio builders made their own smaller Leyden jars using everything from juice jars to test tubes. Welch's jars were said to be a favorite. They were not the only capacitors at this time. Industries that needed low-voltage capacitors, like the telegraph people, used early paper capacitors. Invented by Fitzgerald, paper capacitors had been around since 1876. Marconi wrote of using simple waxed paper and foil capacitors (and perhaps ceramic). Leyden jars, however, could handle many amperes and 10s of thousands of volts for early radio transmitters which the others could not.
The German government subsidized its Leyden jar industry, helping give Germany a near monopoly. Their performance was exceptional. Different glass formulations had different amounts of loss (ESR) and the glass formulation the Germans used, a type known as "Bohemian glass", had a lower loss than other countrie’s glass. This worried the British Navy; a likely enemy government had a strangle hold on their communications. In this they were right, WW I ended the supply of German Leyden jars. Another problem is that Leyden jars were not the most robust devises. They were large and fragile, not what you want on a ship. The glass was thin to increase the capacitance and the concussion of a naval gun might break it. Even the best Leyden jars ran hot and so required ventilation, heat generation prevented them from being operated at a 100% duty cycle, they generated ozone, and had a limited life (often less than a year). Some are said have been put in metal containers under vacuum to eliminate the ozone.
In the years before mica capacitors, people often used flat-plate glass capacitors to replace the Leyden jars, usually in oil. These were more robust than the jar design but didn't improve the ESR. Glass plate capacitors could be repaired on the spot by replacing a punctured plate. But apparently, the plate type is more subject to a kind of arcing called "brush discharge" (what we would call corona) that limits the life of glass capacitors. The two types were sometimes used in the same transmitters at times. The Leyden jars might be more suitable for some applications than the plate capacitors. Around 1902, Ignacy Mościcki (Poland) designed a water cooled tubular glass capacitor suited for very high voltage, to 100,000 volts. Other people also built tubular glass capacitors.
Mica:
Along came William Dubilier. Dubilier (1888-1969) was a New York boy with an interest in radio. His
goal was to make a small, rugged, and affordable radio for airplanes. Such a radio would benefit from
small, rugged, and affordable capacitors which Leyden jars were not. People had been speculating on more
practical high voltage capacitors for some time and there was general agreement that muscovite mica would
be a good material. Mica had been studied and actually used in capacitors for over 50 year but it was a
tricky material and it took the rise of radio plus the onset of war to push its development. Tesla had
designed an early mica capacitor vacuum impregnated in oil (464,667) in 1891. Actually, the patent seems
to cover mica, glass, and other dielectrics. Some people seem to think it even covers paper-in-oil, the oil
being the patented part. In 1910 Dubilier, made a crude mica capacitor for high voltage operation, but with
an eye to develop a better, more reliable part suitable for replacing the inefficient and unreliable glass
capacitors. Dubilier showed it to the Navy that year, but it broke down in testing. Dubilier was probably
trying to get money for further development, but the Navy was not impressed and gave it a bad report. In
1913 Dubilier demonstrated a mica capacitor to the British War Office. They were more impressed. It was
much smaller and more efficient than the set of Leyden jars it replaced and they thought it had promise.
In the next few years mica capacitors were developed and manufactured in England by Dubilier and his
British co-workers. This was not easy. A myriad of design and manufacturing problems had to be solved
to make a practical part. For example, mica is something you dig out of the earth and can have a variety of
defects, such as pinholes, cracks, air pockets, and inclusions. A fast and efficient way of testing each plate
had to be devised. A single capacitor might use 1000 plates, each about .002" thick. This and other
problems were overcome however, and the Dubilier Condenser Company would go on to make so many
mica capacitors that it would greatly drive up the price of quality mica and cause serious supply problems.
They used about 50 million plates one year. Dubilier became the first company to make a true mass market
capacitor but it was soon followed by others.
Mica was a big improvement over glass, lower ESR, no more ozone, no more brush discharge, much longer
life, small size, and very rugged. Eventually, Dubilier even made them self-healing. Yet mica capacitors
didn't totally take the radio world by storm. Leyden jars got better over time and remained cost effective in
some applications because mica capacitors were expensive. Also there was a long running mistrust of mica.
Some people used Leyden jars into the 1920s. Leyden jars are not dead even now. Hobbyists still use
beer bottle and test tube capacitors for high-voltage experiments.
In years to come, mica capacitors would become one of the mainstays of electronics and small parts are
available to this day. Larger mica capacitors made of large plates would be made in declining numbers.
High quality muscovite plates have limited availability and most of the world's supply has been used up.
Today, large mica capacitors are still made, but of mica paper, micas flakes bonded with a variety of
adhesives (epoxy, silicone, and polyester).
Paper in oil:
D. G. Fitzgerald was issued a patent for a paper/foil capacitor (with paraffin wax) in 1876. Like other early capacitors, these were more a laboratory curiosity than something ready for mass production. However, there was some early production of paper capacitors. Marconi described a tuning capacitor made of metal foil and wax paper. There is a suggestion that some early paper capacitors may have used just paper and no oil. There were a variety of of commercial impregnated paper materials such as Westinghouse paper and Pertinax. In any case, paper proved to be as tricky a material to work with as mica, and Dubilier Condenser Company seems to have been on the cutting edge once again. An early version used powdered metal as the electrodes but was not reliable and was eventually replaced by metal foil. This type of capacitor was patented by George Mansbridge in 1902. The capacitor on the right is one of those. A thin foil worked much better, but there was a problem in making foil thin enough in lengths of more than a few feet at this time. In the 1940s, the German company, Robert Bosch GmbH, worked out a method of vacuum depositing zinc directly on the paper. At about the same time, A. H. Hunt in Britain was doing the same thing with aluminum. Each metal has its advantages and disadvantages and both are still in use today, sometimes in combination (Dubilier, 2,982,012). These capacitors, like the later metallized film parts, had a self-healing capability. The paper came to be impregnated with a variety of oils and waxes. They include petroleum products, chlorinated products (PCBs and others), silicone oils, and vegetable oils. By 1950, some people were using solid impregnants like Aerolene from Aerovox, a polyester resin. Reliability was improved by coating the paper with cellulose acetate.
There were many problems in making paper capacitors practical. The paper needed the right moisture and ash content, even the right pH. The oils and waxes needed a very high purity, and only certain kinds worked well. The manufacturing environment had to be very clean of foreign materials like metallic particles. Linen based paper was used until the 1940s when Bell Labs found that wood based paper had a much longer life under high voltage/high temperature conditions. This was critical for military electronics. Bell Labs isolated the actual chemical that prolonged capacitor life and it was used as an additive. Bell Labs passed this information on to their competitors who also made parts for the military.
Paper-in-oil capacitors became much better but never were totally satisfactory. Moisture absorption was always a problem except for the hermetic parts, but many were sealed in only wax and cardboard. Performance in general was never as good as modern plastic film capacitors. Temperature and frequency drift, dissipation factor, long-term drift, volume efficiency, and leakage were all poor by the standards of later plastic capacitors, especially for the non-hermetic parts. Many oils had particularly poor performance at low temperature. They became good enough however, and were a mainstay in electronics through the 1950s when plastic film capacitors began to appear. Small paper and film/paper hybrids were being made into the early 1980s. A few companies still make medium sized PIOs and hybrids for large power supplies. PIO capacitors are widely used in high-voltage/high-current applications, usually as hybrid parts. Epoxy-impregnated metallized-paper capacitors are used in some X line-filter capacitors.
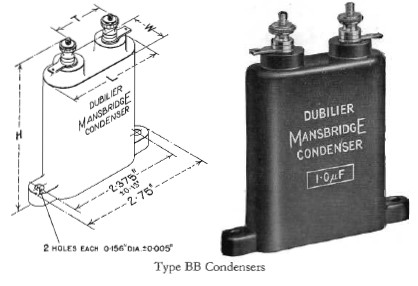
Paper capacitors from 1928.
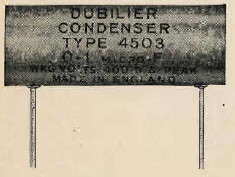
Air variable:
Marconi wrote about his variable capacitor which was just wax ("paraffined") paper and metal foil. Tesla included a variable capacitor in patent 464,667 in 1891. The first modern variable was patented in Germany in 1893 by Hungarian Dezso Korda. It looked much like the variables that would be standard in years to come. There were however, a variety of other designs, both continuously variable and switched, some with oil or Ebonite (a kind of hard rubber) used for the dielectric.
Hammarlund Manufacturing Co. is given credit for standardizing the design of the air-dielectric variable capacitor. They were one of the largest manufacturers in their time, although there were many others early on, including Dubilier. During WW II, tens of millions of their APC line of variable capacitors were made by them and other manufacturers. Hammarlund has been gone since the 1970s, but NOS Hammarlund variables are still around in significant numbers and Viking Technologies still makes Hammarlund part numbers. An APC-50 is shown below. The "50" means it's adjustable from several pF to 50 pF.
Japanese radios once used variable capacitors with a film dielectric before electronic tuning replaced them. Film variable capacitors still have limited availability.
Vacuum and gas:
The vacuum capacitor was patented by William Dubilier for Dublier Condenser Corp (1,738,175) in 1925. It's not clear Dubilier Condenser ever manufactured them however. They are high-current/high-voltage capacitors suitable for transmitters and other high-power rf equipment. They first appeared for sale in the 1930s. Eimac (Eitel-McCullough) was the first manufacturer I know of (1938), but they were soon followed by others. Probably anyone who can make a vacuum tube can make a vacuum capacitor. Variable vacuum capacitors seem to have appeared around 1945. Pressurized gas capacitors were already is use before 1920. Early gas capacitors were made by transmitter manufacturers but were unreliable and prone to unexpected failures. By 1940 they were available from equipment makers and included variable ones. They are still used in transmitters and are especially popular for HV calibration capacitors and capacitive voltage dividers.
Aluminum electrolytic:
Aluminum/aluminum oxide electrolytic capacitors went through a long development history. The first electrolytes were boric acid, sodium borate, and ammonium borate used in various combinations in a water solution. An important patent was granted to Karol Franciszek (Charles) Pollak in 1896. He used plain aluminum at first, but Pollak realized that etching the sheets would greatly increase the capacitance by increasing the surface area. Variations on this theme were used through the 1920s. Spraying molten aluminum on a carrier substrate was an alternative process that came and went. He was also the first to use an alkaline electrolyte which gave the oxide layer a much longer life than previous acidic electrolytes. These were all called "wet" electrolytes. In the 1930s solutions based on various glycols and amines were brought into use by Samuel Rubin with a 1930 patent. These were called "dry " electrolytes because they contained only a small percentage of water. Rubin, was also the first to use stacked foil and paper construction, much like the later wound construction. Ruben, a prolific inventor, has been called the "father" of the modern aluminum electrolytic. Aluminums still had poor reliability until WW2 when enough money could be spent to work out the last major bugs.
Tantalum electrolytic:
The first tantalum electrolytic capacitors were made in the 1930s by Transitor Electronics for the military. They used tantalum foil, with a sulfuric acid electrolyte, in a silver case. Very expensive. Bell Labs came up with a sintered tantalum powder, in the early 1950s (Haring and Taylor), with other electrolytes including manganese dioxide (Power and McLean) . Solid electrolyte tantalum capacitors from Sprague Electric appeared for sale around 1956. Robinson and Millard at Sprague had worked out the final manufacturing problems. In the 1990s several companies introduced electrolytes of conductive polymers. These have conductivities much higher than manganese dioxide for lower ESRs. High tantalum prices have caused some manufactures to use niobium capacitors at various times. Niobiums are similar to tantalums but with a lower temperature range and lower voltage range.
Ceramic:
Ceramic capacitors were being investigated in the same time frame as paper and mica, at least as early as 1900. During WW I the Germans investigated ceramic materials as a replacement for Leyden jars because they had problems making reliable mica capacitors, and during the war, quality mica was hard for them to get. The Germans even made copies of the Dubilier capacitors but lacked the experience to get the details right so they were not reliable. By the end of the war they had ceramic capacitors that were claimed to be about as good as the best mica parts for use in transmitters. This gave Germany a lead in ceramic capacitors for higher frequency radios that came into use in the 1930s. These ceramic materials had names like Calit and Ultra-Calan and were probably similar to modern Class 1 and 2 ceramic materials. Around 1925, titanium dioxide came into use, and products appeared in the early 1930s. This was important because TiO2 is used in small, high performance ceramic capacitors. Barium titanate (BaTiO3) was first used in 1941 and had a much higher dielectric constant for smaller, higher value capacitors (although lower quality). These were followed by a wide variety of other ceramic materials.
Plastic film:
The first attempt at a plastic film capacitor may have been cellulose nitrate in the 1910s with the first becoming widely available in the mid 1950s. There was a virtual explosion of plastic capacitors in 1955, although the first were seen in the mid 1940s. Mylar (polyester), polystyrene, and Teflon were the first, sometimes alone, sometimes in a hybrid with paper and/or oil. Some capacitors were advertised as just "plastic". Other polymers were soon used as well. Polypropylene was introduced in the early 1960s by GE and became a favorite for high-current AC applications as well as small parts. Polyethylene on the other hand, was considered for its exceptional electrical properties but rejected for its very poor heat resistance. Polycarbonate appeared in the mid 1960s.
Other capacitors:
Small, solid, glass capacitors appeared in the 1950s, first made by Corning and Vitramon. The early ones were color-coded like micas. They are now made by AVX and are still used in space applications.
Nomenclature:
The word “condenser” was first used by Alessandro Volta in 1782. The idea was that the “electrostatic force’ was being “condensed” by the Leyden jar. People started to refer to condensers as "capacitors", at least as early as 1926. The use of capacitor seems to have originated in the United States and the U.S. Navy was an early adopter. The British had become a bit annoyed with us for spawning new words and units where they saw no need. They did however approve of the adoption of "capacitor". The word capacitor was being used by Cornell Dubilier in the mid 1930s while some companies were still using condenser into the 1950s. Condenser has some usage even today. How did this change happen? Maybe because while condenser was the name of the device, the value was being called "capacitance". And maybe condenserance just didn't sound right.
The Farad, named after Michael Faraday, was proposed in 1861 by Latimer Clark (of Clark cell fame) and Charles Bright, and made official in 1881. Clark and Bright lead the adoption of the names and definitions of electrical quantities and their inclusion into the metric system. The "jar" was used into the 1920s and by a few people, even beyond.
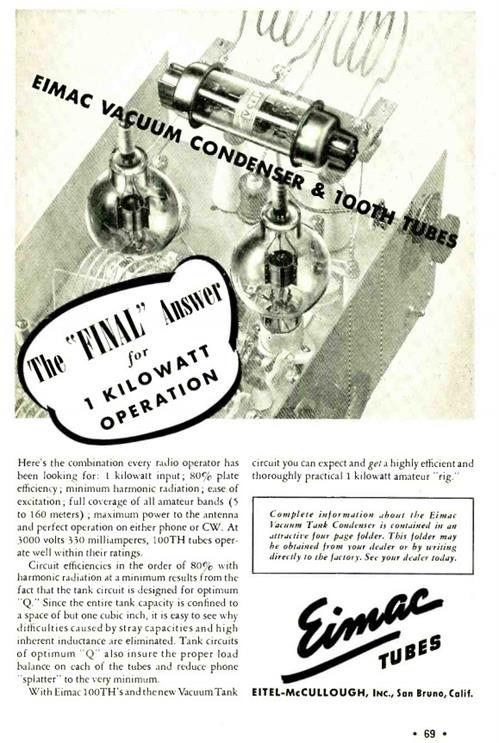
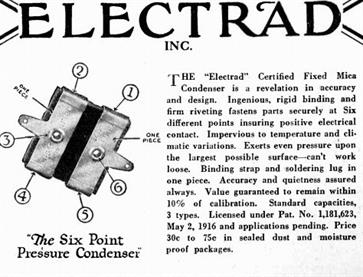
There is a lot of bad information on the internet and I'm sure some of that is included here. Also, this page is kind of US/GB-centric, English being the only language I know.
Acronyms used on this page:
NOS: New Old Stock
PIO: Paper in Oil
This is from 1938 and may be the first ad for a vacuum capacitor.
Much Ado about Almost Nothing, Hans Camenzind. History of electricity. The capacitor is mentioned only once.
What I have found interesting is how quickly scientists dealt with capacitors with what might be considered "modern" thinking. By the beginning of the 20th century they already understood dielectric value drift, leakage, frequency, and ESR. They were researching the affects of time, temperature, humidity, and radiation. There was even papers written that described dielectric behavior that would eventually be known as dielectric absorption.